MSA Safety - Tracking items through managed services
By implementing an RFiD Discovery system to track uniform items through their managed services, Bristol Uniforms have cut the time it takes to collect and deliver items, reduced costs of replacing lost items and improved service visibility for their customers.
Bristol Uniforms is one of the world’s leading providers of emergency services protective clothing, supplying garments and personal protective equipment (PPE). Customers include over 30 fire brigades in the UK, half of which subscribe to a managed service for the repair, cleaning and maintenance of uniform items.
Challenges
Prior to implementing RFID tracking and with uniform items regularly being moved to and from the fire services which are using them, Bristol Uniforms faced a number of challenges:
- When collecting garments drivers used to have to remove them from a bag and manually barcode scan each item which was time consuming and occasionally could lead to errors.
- With a lot of deliveries being made to un-staffed fire stations, there was no way of proving that an item had been delivered.
- There was not enough visibility of where items are, and misplaced or lost ones often had to be replaced causing unnecessary cost for Bristol Uniforms.
- Ensuring that the right garments were returned to the correct location was a challenge.
Solution
In April 2016 Bristol Uniforms introduced an RFiD Discovery system to complement manual barcode scanning in tracking the locations of PPE items supplied to Cambridgeshire Fire and Rescue through the maintenance and repair processes.
Now the company is tracking all 218,000 items of uniform which are provided as part of their managed services to around different 15 emergency services around the UK.
Managed services clients also include London Fire Brigade, one of the largest firefighting and rescue organisations in the world, for whom the RFiD Discovery system tracks nearly 60,000 items of uniform.
The biggest difference RFiD Discovery has made is helping us reduce the number of lost and misplaced garments and therefore avoiding the cost associated with replacing them.
RFiD Discovery gives us a lot of data in real time for minimum effort.
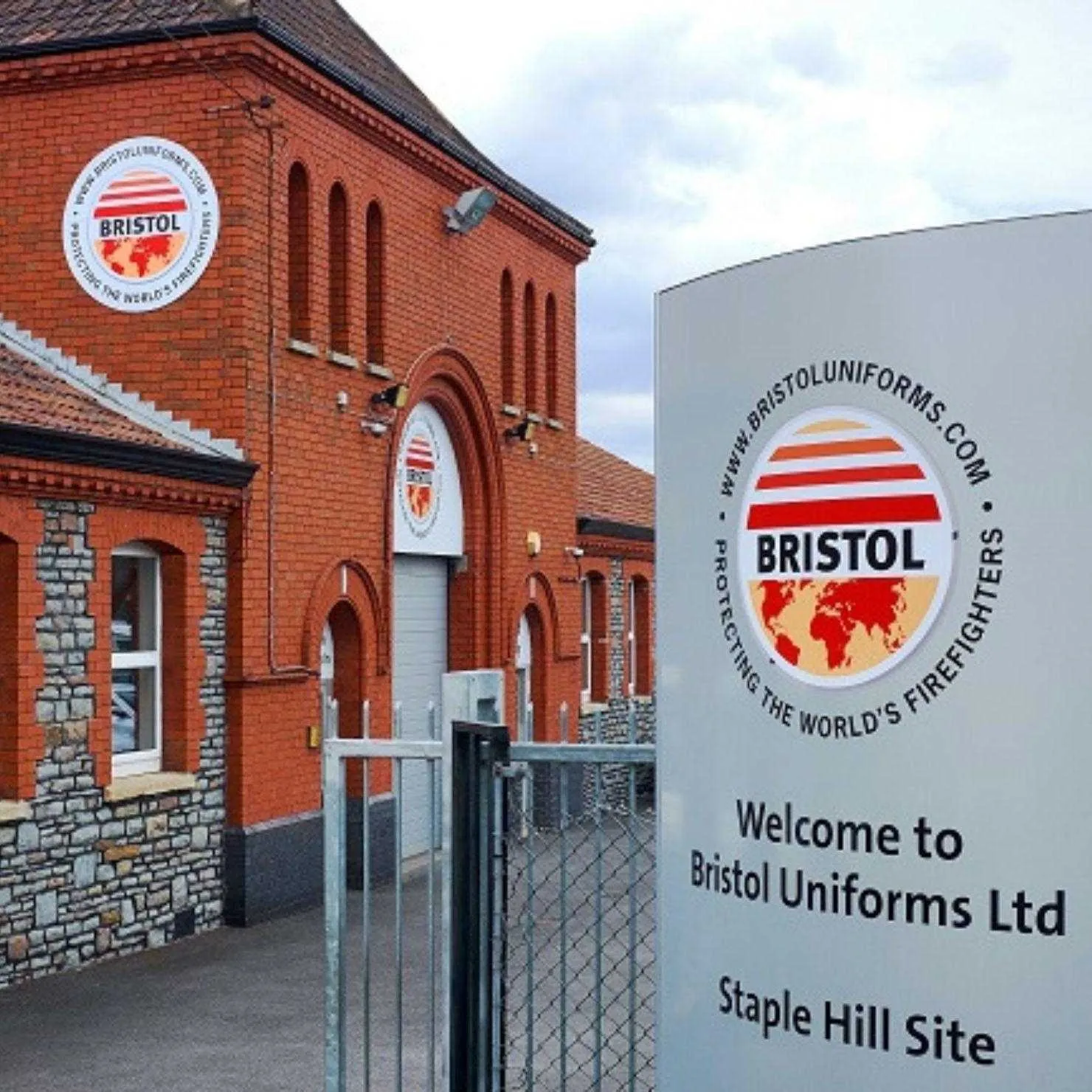
We were impressed with the simplicity of the process and how easy it is to use the system. At the time RFiD Discovery was one of only a few technology providers and they really understood our requirements from the beginning.”
Key Benefits
- More control over assets
- Reducing cost of replacing lost and misplaced items
- Saving time by eliminating barcode scanning
- Proof of delivery to settle possible disputes over non-deliveries
- Better visibility of item location for customers
How does it work?
Each newly manufactured uniform item is fitted with a passive RFID tag to enable the automatic tracking of items through the managed services care programme.
The waterproof fabric RFID tags are securely sewn into a pocket in each garment, whilst self-adhesive RFID labels are applied to hard items such as helmets. Fabric tags can withstand temperatures of up to 180 degrees, which means they survive in most fire-fighting conditions as well as during professional cleaning procedures.
Each uniform item is scanned using one of 12 handheld RFID readers at key points of the managed services process, including at point of collection from the fire station through to return delivery. Edward adds:
“RFiD Discovery gives us a lot of data in real time for minimum effort.”
The outcome
Thanks to RFID, collecting items from a fire station is now much quicker. While it used to take on average 15 minutes to barcode scan a full collection bag of uniforms this can now be done in seconds providing a complete audit trail of assets. With nearly 200 collections a day, this adds up to around 45 working hours saved every day!
As Bristol Uniforms regularly delivers to unmanned or small fire stations, there is often no one there to receive and sign for items. RFID provides the evidence that items have been delivered to settle any disputes, so unnecessary costs for replacing lost or misplaced items are reduced. Edward comments:
"The biggest difference RFiD Discovery has made is helping us reduce the number of lost and misplaced garments and therefore avoiding the cost associated with replacing them.”
Bristol Uniform’s customers now also benefit from being able to access an on-line database which shows the list of their uniform items with location against each fire fighter’s name.
In addition, RFID tracking plays a vital role in proving that Bristol Uniforms achieve agreed KPIs and meet SLAs with regards to how quickly they can carry out maintenance or clean uniform items, such as a 7-day turn around for repairs.
Plans for the future
In December 2019, Bristol Uniforms had a fixed RFID reader installed, which automatically detects uniform items which come onto the premises through a shutter door.
Edward concludes:
“RFiD Discovery has definitely worked for us, and we will be integrating RFID into our next generation of PPE. We are looking to increase the number of garments tracked, and are considering installing more fixed readers for automatic data capture.”