How Plymouth NHS tracks 40,000 medical devices
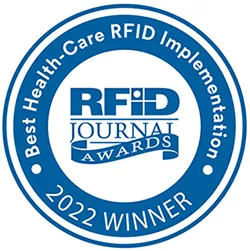
Since installing the largest GS1-compliant RFID track and trace solution in the entire NHS to track 40,000 medical assets, University Hospitals Plymouth NHS Trust (UHP) is seeing substantial benefits throughout its organisation.
As a result, the trust has received a large amount of recognition in the industry and beyond, including winning the prestigious RFID Journal global award for Best Healthcare RFID Implementation.
The project began against the challenges of the COVID-19 pandemic, and saw over a third of the hospital’s medical devices fitted with GS1 compliant passive RFID tags. With the implementation now nearing completion, today it represents one of the widest uses of RFID technology in healthcare. The new system has led to instrumental change, helping the largest hospital in the Southwest of England improve operational efficiency, cut costs, and improve patient safety.
Real-time visibility of assets
The benefits of RFID technology as a fast and accurate way to capture asset location data are already being demonstrated at UHP, helping to locate devices in the hospital’s large 12-floor building.
120 fixed high-performance Impinj Speedway readers are responsible for tracking the location of 25,000 medical devices, 5,000 sterile services assets as well as 10,000 IT assets which are currently being added to the system. The system is now tracking the entire database of tagged assets to reduce the time clinical staff and technicians spend looking for equipment. It is also helping to improve device availability, reduce costs associated with unexpected device failure, while helping the hospital to meet its all-important goal of improving patient safety in line with the NHS Scan4Safety scheme.
How does it work?
Passive RFID labels, fully compliant with GS1 standards, are fitted to each item to be tracked, replacing the existing asset labels. They are encoded with a unique ID which is linked to a particular asset in the database on registration. Unlike active tags, passive RFID tags do not require a battery but use an external power source to trigger a signal transmission such as a mobile passive RFID reader or a network of fixed readers. Signals received by the readers are then passed to a central database which provides location information to clinical staff and medical engineers.
Being able to locate devices quickly with RFID will continue to deliver positive impacts in the long-term. For example, ward audits are already taking 90-95% less time, saving the Trust an estimated £10,000 per year on manual contracts.
"The system has been hugely beneficial for us by tracking devices as they come and go, enabling us to see whether they are actively in use. Even more crucially we can now see at a glance what is in stock, saving clinical staff a wasted trip.
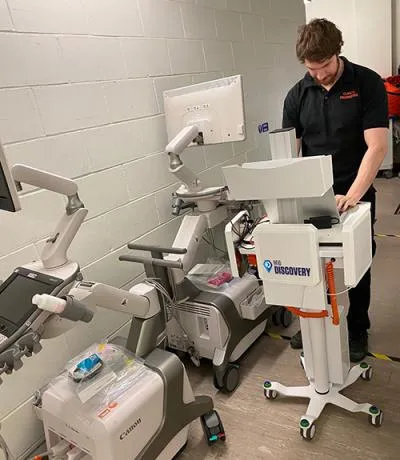
In addition to its large network of fixed readers, UHP also uses two different types of mobile passive RFID readers. This includes 10 RFID-enabled smart Android handheld scanners with a read range of up to six metres, which are used to locate specific equipment.
The Trust also uses two mobile trolleys, each equipped with an Impinj reader to detect tagged assets and inventory as it is pushed around the hospital site, with a read range of up to 11 metres. Together the mobile solutions offer a quick and efficient way for the hospital’s engineering and technical teams to regularly perform audits internally and within departments and wards.
Powerful real-time location
UHP is one of the six demonstrator sites chosen by the Department of Health and Social Care (DHSC) in 2016 to take part in the world-first Scan4Safety programme. The ambitious project was initiated to demonstrate the implementation of GS1 and PEPPOL standards in the NHS. Over a two-year period, UHP has successfully worked to implement standards, barcodes and a common way of working to improve operational efficiency and increase patient safety.
Through the use of GS1 compliant labelling, the Trust has also been able to dedicate more time to patient care and reduce inventory levels throughout its organisation.
With over 120 fixed readers and 350 connected antennae, combined with mobile readers and connected interfaces, the system deployed at UHP constitutes one of the largest and most dense passive RFID reader infrastructures in a hospital in the UK, capable of providing powerful real-time location information with the potential to save millions of pounds every year.
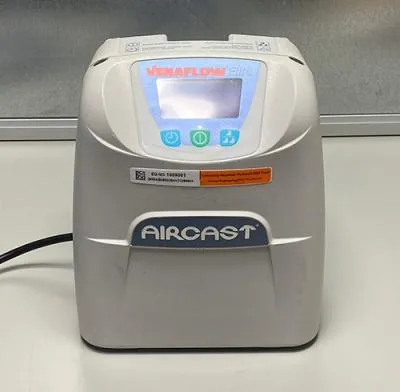
Key benefits
- Reduced time spent looking for devices
- More time for patient care
- Real-time visibility of available devices
- Improved planned preventative maintenance (PPM) and compliance rates
- Time to audit devices reduced by 90 to 95%
- Valuable data for future planning
Helping locate devices quickly
One of the key ways the system has proved most valuable is in helping to locate devices quickly, ensuring they are available in the right place at the right time for patient care.
Alex Peters, Medical Asset Register Developer at UHP said: “The difficulty in locating devices led to situations of devices not being available when needed. The uncertainty of device availability meant that wards would hoard equipment, which exacerbated the problem even further. Having visibility of device locations through a central tracking system helps to effectively solve this challenge.”
The system has also helped manage thousands of newly purchased critical care devices such as ventilators at a time when it was essential to maximise equipment utilisation. It has further supported the hospital’s infection control efforts by providing visibility of devices coming from COVID suspected wards to ensure these were dealt with appropriately.
Increasing compliance
With the RFID system assisting engineering staff in locating devices due for maintenance, the technology has also helped to increase compliance and reduce the chances of equipment failure.
Internal services including the Trust’s Clinical Engineering department rely on upholding this compliance to be able to maintain their status and attractiveness for maintenance contracts with external private customer sites across the South-West of England. These contracts currently provide an income worth £360,000 per year for the organisation.
Reducing delay
Another huge benefit of the RFID system is a reduction in the delay of patient treatment and the associated costs resulting from equipment not being available when needed.
The latest reports show that bed blocking in hospitals has increased by 42%, and the average patient stay costs £400 per 24 hours. Lack of medical equipment when needed – or time lost when searching for devices – contributes to these delays. The Trust estimates that by reducing the amount of time a patient stays in the hospital by just 1 hour per discharge, the potential savings could be £620,000 per year.
Furthermore, the Trust was spending £46,000 a year on loaned equipment. A huge percentage of this cost was down to not being able to locate equipment when it is due to be returned, resulting in unnecessary additional fees. Being able to track and ensure the timely return of loan devices is now reducing hire costs by an estimated 30%, which would equate to potential savings of £15,000 per year.
Reducing time, cutting costs
"Being able to locate devices quickly with the help of RFID tracking will continue to deliver positive impacts in the long-term for UHP”, Alex says. "For example, ward audits are already taking 90-95% less time, saving the Trust an estimated £10,000 per year on manual contracts.
“The initial re-labelling effort also provided a ‘clean sweep’ audit. Tagging 25,000 medical devices provided an excellent opportunity for intense manual scrutiny to locate millions of pounds worth of equipment.
Improving patient care
Meanwhile, cutting the significant amount of time spent looking for equipment will continue to reap positive rewards, with the potential time savings even bigger for clinical staff.
According to a Nursing Times Survey, nursing staff spend an average of one hour per shift looking for equipment. With the hospital currently employing 2,500 nurses and healthcare assistants, internal estimates predict that staff could save over 3,850 hours per week looking for devices. This equates to more than 100 full time nursing staff who would then be available to dedicate their time to patient care instead.
Since reaching near-complete implementation of the project, staff are already spending an estimated 50% less time looking for devices, equating to savings of up to £20,000 a year for technical staff, with potential for £2.6 million annual savings for the clinical team once the Trust-wide training programme roll-out is complete.
As we near project completion, we are confident we will achieve even more of the intended benefits to attain our primary goal – to improve patient safety – and ultimately help our hospital save more lives.
What's next?
UHP has already received a large amount of recognition in the industry and beyond for their implementation of RFID tracking technology including winning the Best Global Healthcare Implementation at the prestigious RFID Journal Awards in May 2022.
At present the entire RFID project infrastructure is situated within UHP’s main central hospital building. However, there are already advanced plans to expand this to re-developments and expansions internally and to external sites. Financial approval is already in place for a large Emergency Department expansion and refurbishment, modular theatres expansion at the Royal Eye Infirmary, and the hospital waste hub. There is also additional scope for the estates department (building maintenance), stores, and patient tracking to be included in future too.